What is a force torque sensor?
- yjpark89
- Jan 16
- 4 min read
1. Types of Force Torque Sensors
Force torque sensors are used in robotics to measure or control forces and torques in a 3D space. Torque, in this context, refers to twisting force. These sensors are part of the sensor domain within collaborative robot hardware, along with robotic arms, end effectors (End of Arm Tools), controllers, and drives.
While traditional torque sensors were primarily used to enable robotic joints to move in various directions, force/torque sensors go a step further. They measure forces and torques that robots previously could not detect.
Force torque sensors can be classified as follows:
6-axis force torque sensors (Fx, Fy, Fz, Tx, Ty, Tz): Measure all types of forces and torques acting on a specific point.
3-axis force sensors (Fx, Fy, Fz): Measure forces in three axes only.
1-axis pressure sensors: Measure pressure along a single axis.
Torque sensors: Measure rotational forces along a single axis.
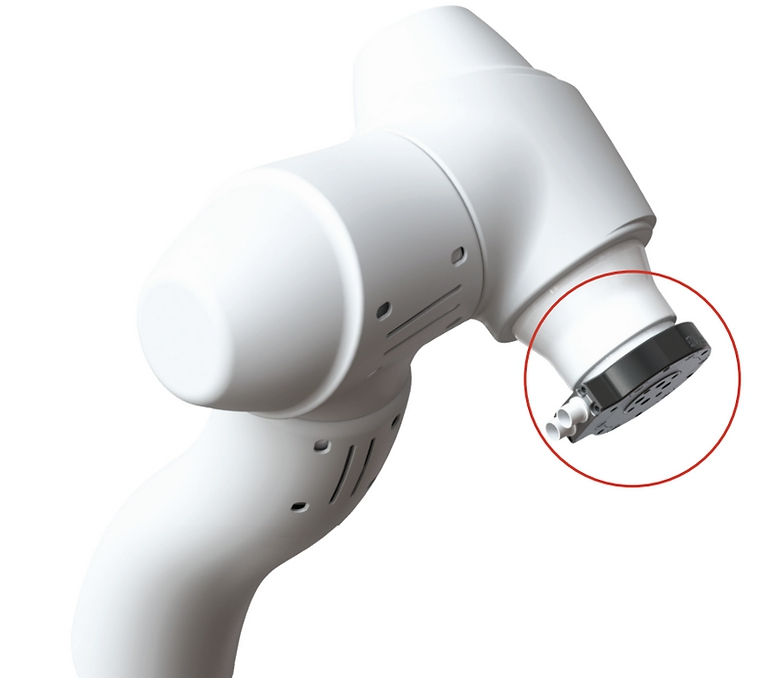
2. Classification of Sensors by measurement method
Force torque sensors can be broadly categorized by their measurement methods into strain gauges type, capacitance type, and etc.
Among these, the strain gauges type employs a measurement method which are film resistors. A strain gauge is attached to the deformable structure being measured, and as force is applied, the strain gauge detects minute resistance changes to measure the force.
Strain gauge type sensors require manual assembly of internal components for measurement. They also necessitate the use of a separate amplifier to amplify the resistance signals. However, they are prone to errors during the resistance measurement process. While they deliver outstanding performance, they are expensive, require an additional amplifier, and involve limitations in accounting for resistance-related variables.
On the other hand, capacitance measurement sensors are more cost-effective but have weaknesses compared to strain gauges. They generally have lower performance and precision and are more vulnerable to external temperature and environmental factors.
Capacitance | Strain Gauge |
Measures force using resistance changes in strain gauges | Measures force using resistance changes in strain gauges |
Relatively inexpensive Lower performance and precision Week for environmental resistance | Excellent performance Very expensive Require another amplifier |
3. AIDIN ROBOTICS’ Differentiated Capacitance Sensing Technology
AIDIN ROBOTICS primarily adopts the capacitance measurement method but has addressed its traditional shortcomings by utilizing the fringe effect technique. This approach allows for precise measurement of distance and area, achieving a level of sensitivity and rigidity comparable to that of strain gauges.
Based on proprietary technology, AIDIN ROBOTICS has continuously advanced its sensor generations, improving sensitivity more than tenfold compared to standard capacitance type sensors. Furthermore, its sensors demonstrate exceptional responsiveness to external temperature and environmental factors, incorporating temperature compensation techniques—a feature that sets them apart from competitors.
This innovation ensures superior performance and competitive pricing, enabling AIDIN ROBOTICS to maintain a technological edge over low-cost Chinese sensor manufacturers. Customers can now reduce reliance on expensive imported sensors, significantly alleviating the financial burden of adopting force torque sensors.
First Generation | Second Generation | Third Generation | |
Image |
![]() |
![]() |
![]() |
Explain | Basic capacitance type | The advanced technology overcomes the limitations of capacitance type | Upgrade the second-generation version |
Feature | - Vulnerability to External Noise - Complex Structural Design for Force/Torque Measurement - Sensitivity to Temperature change - Difficulties in Mass Production Due to Dielectric Material Usage | -Enhanced External Noise Resistance -The advanced Fringe Effect for 10x Increased Sensitivity - Temperature Compensation via Thermal Property Learning - Mass Production Feasibility | - 80% Higher Sensitivity Compared to 2nd-Generation Products - AI-Based Calibration for Improved Accuracy, Repeatability, and Linearity -Next-Generation Temperature Compensation for Enhanced Stability in Temperature and Humidity Variations |
4. Applications of Force Torque Sensors in Various Fields
In the robotics field, 6-axis force torque sensors are commonly mounted on the end effectors of collaborative robots (cobots) or industrial robots. These sensors are used for quality inspection in mass production lines and for processes that require force control, such as surface treatment. Additionally, some collaborative robots are equipped with single-axis torque sensors on each joint to implement sensitive collision detection and safety functions, highlighting the importance of safe collaboration between humans and robots.
As the demand for robots increases, there is a growing need to handle tasks with high precision. AIDIN ROBOTICS force torque sensors, capable of simultaneously measuring multi-axis forces and torques, support robots in performing these tasks efficiently. The company also produces ultra-compact force torque sensors that can be easily integrated into narrow spaces like robot hands, grippers, and VR devices, enabling finer operations.
Once force torque sensors are integrated into collaborative robots, they can be applied to a wide range of manufacturing processes requiring precision, such as grinding, welding, screw assembly, and surface treatment. These sensors offer broad versatility and scalability. The type of sensors used in collaborative robots, as well as in various industrial robots, varies depending on the manufacturing process and product formation of each robot maker. As robot manufacturers apply different sensors based on factors like robot price and product purpose, the types of sensors integrated into robots will become an important factor in customers' decisions when selecting a robot.

In the robotics industry, many acknowledge that robots equipped with these sensors greatly enhance the sophistication and safety of collaborative robots. As the collaborative robot market grows, customers looking to purchase robots will increasingly prioritize high performance and stability. Therefore, robots equipped with force/torque sensors and other types of sensors will make up a larger proportion of the market.
Until now, force torque sensors have been considered a relatively difficult technology to implement in the robotics industry due to challenges related to price, technology limitations, and the complexity of installation. However, as the range of robotic applications expands and products like those from AIDIN ROBOTICS address the limitations of existing strain gauge and capacitance measurement technologies, the adoption of force torque sensors in real-world applications is expected to rise.
This trend is expected to have a significant impact on everything from the precision of robot movements to human-robot collaboration. The advanced force torque sensors developed by companies like AIDIN ROBOTICS will accelerate the sophistication of robots in the market, offering customers more affordable options and ultimately speed up the widespread adoption of robots.
Comments